I saw a picture of a wooden box and I was intrigued by the unusual carving style. The picture showed a box decorated with the hobo and tramp carving style which is famous for simple geometric cuts combined with a layered design. I read the “Hobo & Tramp Art Carving: An Authentic American Folk Tradition” book that inspired me to learn more about the hoboes and their carvings.
The Hobo and Tramp carving style originated in the late 19th and early 20th century when a large community of migrant workers and homeless vagrants were living on the road, navigating the rails, crisscrossing the country, finding an occasional job, and making a few bucks here and there. The Hobo community was quite large – up to a several hundred thousand people; they developed their own lingo, special signs, and, fortunately, a unique wood carving style. This Wikipedia page describes the differences between hoboes and tramps.
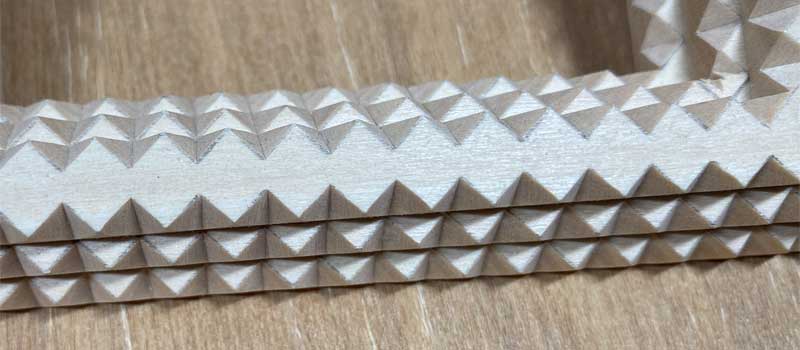
Hoboes and tramps spent their spare time whittling with their pocket knives, and they assembled practical projects such as boxes and picture frames. Hobos sold their carvings or traded them for food. Hobos used any wood they could find to make their carvings and they often reused wood from cigar boxes found in garbage piles. Cigar boxes were commonly made from Spanish cedar, eucalyptus, yellow poplar, white oak, basswood, and some other wood. The hobo carving style is simple enough to apply to any available wood of different densities. Carving small incisions on thin boards is easy on almost any wood. Some hobos assembled very unique guitars from cigar boxes that you can see on this Wikipedia page.
Hoboes carved notches on flat strips of wood and nailed those strips in layers as a decoration to create unique 3-D looking pieces of art. Please google images to see Hobo projects.
I am currently working on the picture frame shown below. You may see some uncarved notches on the top layer of the frame. I drilled the holes in the corners to align the layers with thin dowels.
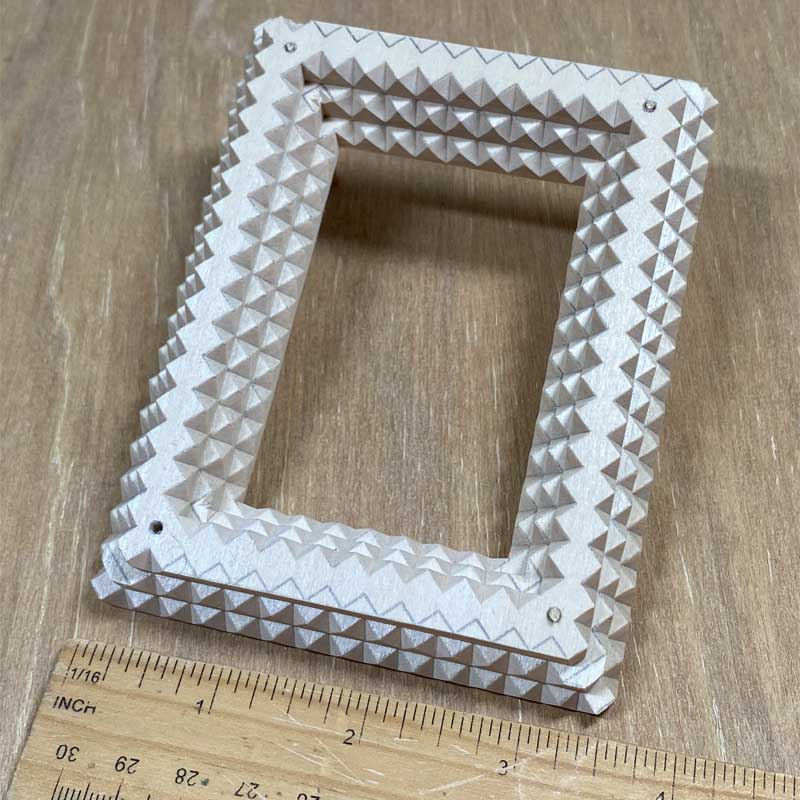
The frame is carved and assembled from three layers of basswood. The size of the frame is 3.5” x 4.5” (9 x 11.5 cm). See a ruler below the frame for the reference.
I am planning to add an easel back to the frame. I will share the finished piece a little later. I would invite you to find a book or two and learn more about the distinctive hobo and tramp carving style.
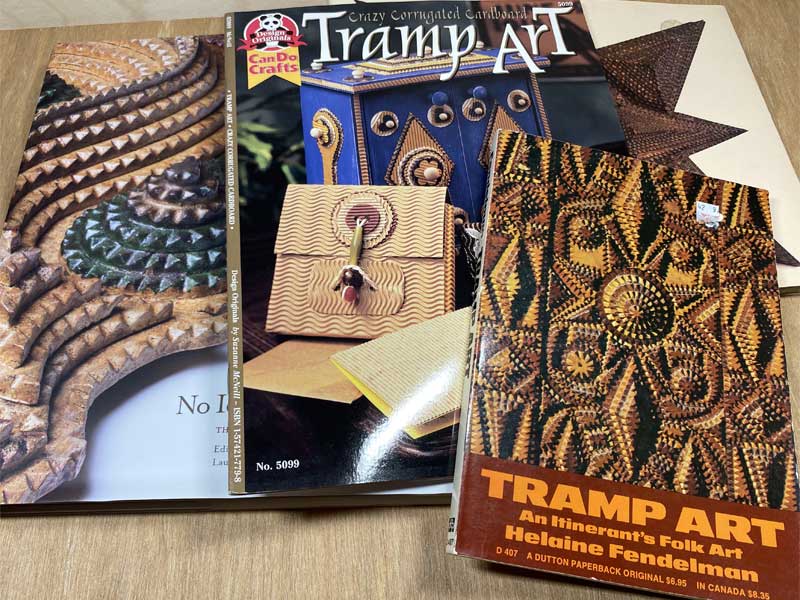
Please let me know what you think about the Hobo and Tramp Art in the comments below. Thank you and happy carving!